System description
wolfseal fresh concrete bond-system
Developed for maximum safety with the simplest processing – with general proof of applicability (aA-FBVS).
The use of fresh concrete composite systems (FBVS) in combination with waterproof concrete structures has now become established on the market for high-quality waterproofing of buildings.
The fact is that a full-surface, external fresh concrete composite waterproofing system in conjunction with a white tank is the best way to protect a structure in contact with the ground from penetrating water in the long term.
The wolfseal fresh concrete bond system is based on an installation and joining technique suitable for construction sites. The possible applications in adverse weather conditions make the system unique.
Bituminous-adhesive bond
The wolfseal fresh concrete bond sealing membrane consists of an
elastomer bitumen with a sanding on the composite side. The sanding prevents the stored sealing membrane from sticking together and allows it to be walked on when laid. When the cement paste comes into contact with the wolfseal fresh concrete bond waterproofing membrane, a bituminous-adhesive bond is formed.
General building inspectorate test certificate available (abP)
Tested for watertightness and rear run resistance
Simple, quick installation thanks to overlap marking
High strength and resistance
thermally joined seams
Processing by trained personnel possible
Resistant to organic waste water
No wave formation, therefore secure seam connection
radon-proof
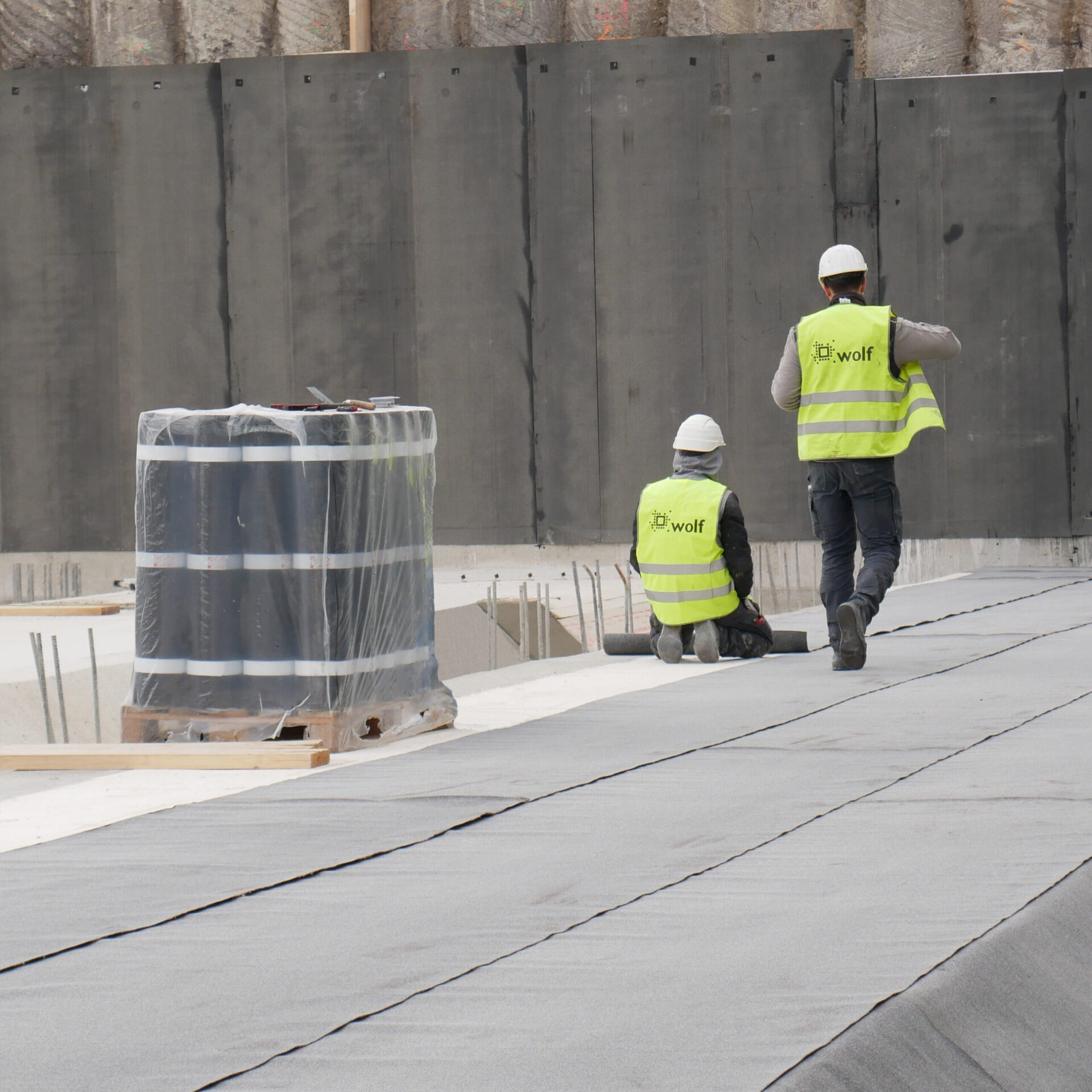
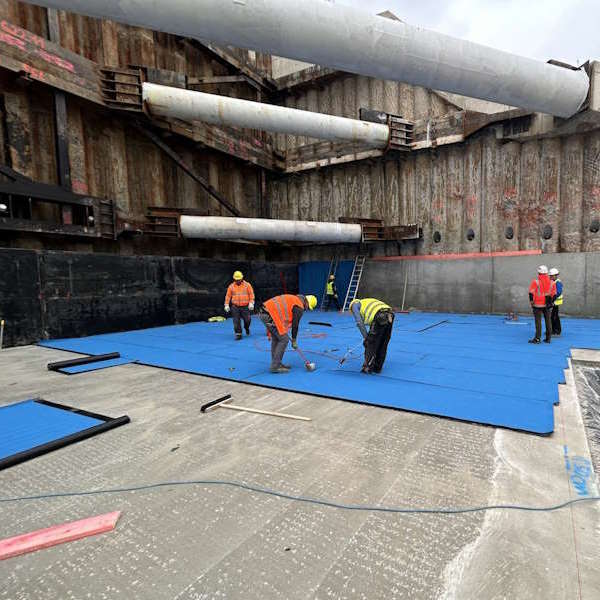
Until now, there was no recognized set of rules for the use of fresh concrete composite systems (FBVS) on construction sites. The new DBV Code of Practice for “Fresh Concrete Composite Systems”, which was published in the fall, was developed to close this regulatory gap. The objective is clearly defined: The jointly developed set of rules should develop into a recognized rule of technology (aRdT) in the future.
It defines standards for planning, tendering and construction that serve as a binding basis for all parties involved. With the introduction of this data sheet, there are now clear specifications for the use and processing of FBV systems on construction sites. The requirements for an FBV system have also been defined with 22 basic tests. The “general proof of applicability” for FBV systems (aA-FBVS) is to become the standard for all products on the market in future.
Load classes & design variants
The clearly defined design variants should be used consistently from the design planning to the realization of the waterproof concrete structure. However, it remains unchanged that fresh concrete composite membranes should never be planned or used as the sole waterproofing, but always in combination with a white tank. It is up to the project planner to decide which variant to use. The DBV has provided many helpful selection lists for this purpose.
– In the “additive” FBVS-1 design variant, full responsibility for a functioning seal lies with the waterproof concrete structure. Any irregularities in the additional FBV system are rectified by subsequent crack injection.
– With the “compensating” FBVS-2 variant, both the waterproof construction and the FBV system must jointly ensure water impermeability. The FBVS is assigned greater responsibility here. A maximum of two white tank requirements can be dispensed with here. Nowadays, the lack of accessibility is a criterion that can be compensated for by a compensating variant.
The selected design variant must be specified in the contract.
Requirements & implementation planning
The overall coordination of the WU planning, including the selection of the suitable FBV system, is generally the responsibility of the project planner, who should in particular take the following planning steps into account.
- Requirements planning and coordination with the client
- Determination of the usage and load classes
- This results in the selection of a suitable FBVS
- Planning of all details
- Preparation of the tender documents
- Planning of FBVS processing and selection of the certified processor
Processing the FBV system on the construction site
The installer must check the plausibility of the overall coordinator’s work preparation in advance. It is important to discuss all site-specific details, such as penetrations, together before starting the construction work.
The overall coordinator must now also adapt his concrete construction concept to the concrete construction qualities (BBQ) of the FBVS and communicate these adaptations with the processor.
The processor must provide evidence of his qualifications by undergoing theoretical and practical training and obtaining a certificate.
Constant monitoring of the installation work is also an integral part of the FBVS. For this purpose, the joints must be continuously checked for suitability using special testing equipment.
At first glance, the extensive 162-page fact sheet can seem overwhelming.
But don’t worry, we’re here to guide you through the process and help you implement the fact sheet, no matter what stage your building project is at.
You might also be interested in
Are you planning a building and need support with waterproofing?
Then get in touch. We are happy to support you.